Hesperian Health Guides
Making the printed circuit board
HealthWiki > Workers' Guide to Health and Safety > Chapter 4: Electronics factories > Making the printed circuit board
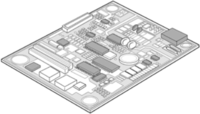
The chips, or integrated circuits (ICs), are attached to a larger panel called a printed circuit board (PrCB). The PrCB and many other components (parts including ICs, electrical connections, and transistors) together make the electronic product. Many of the processes to make a chip are used to make a PrCB, so many of the dangers, such as photomasking, etching, and adding more layers are similar but on a larger scale.
Any time larger quantities of chemicals, metals, or potentially dangerous processes are used, it is more likely workers will be harmed. It also creates more waste and pollution.

Contents
Making the board
The printed circuit boards are made of fiberglass epoxy (a thin plastic sheet that contains threads of glass to make it stronger) and a thin sheet of copper pressed on each side. Sometimes aluminum, nickel, and other metals are used.
Excess copper is stripped from the board to leave behind metal connections for the components. Different kinds of boards are used: 1-sided, 2-sided, and multi-layered (with electrical connections inside and components on the outer sides).
Dangers of Photomasking PrCBs
PrCBs go through a photomasking process that covers the areas of copper required for the design. This layer over the copper hardens when exposed to UV light, leaving the unwanted material soft and easy to remove.
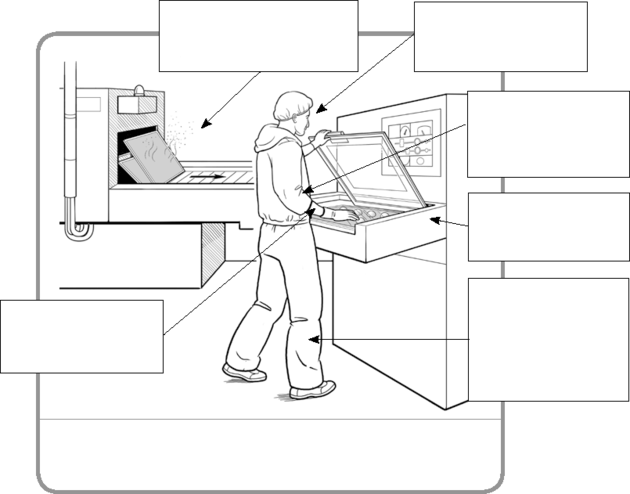
- Good ventilation is needed to protect workers from being exposed to photomasking chemicals while working with this machine and when handling PrCBs after they come out of the machines.
- Workers need protective equipment including chemical-resistant clothing and UV glasses. See Chapter 18: Personal protective equipment.
- Shock-absorbing mats to stand on and enough rest breaks will prevent muscle pain and strain and overuse injuries (see Chapter 7: Ergonomics).
Dangers in the DES (Develop, Etch, Strip) Processes
A conveyer belt usually moves the printed circuit boards through multiple machines in the large DES work area. Many chemicals are put on and then removed from the boards, and can create problems for all workers in the area.
First the photoresist is removed with potassium carbonate or sodium carbonate monohydrate. Then the copper is removed with cupric chloride or ammonium chloride. There are several cleaning stages before the last step, which is to remove the hardened photomask that was protecting the copper. All of these chemicals are harmful when you breathe them in or if they get on your skin.
More layers of copper are added during "plating." The boards are clamped on a rack and dipped in chemical cleaning baths and then dipped in either electrified baths to add copper or nonelectrified baths to add nickel. Finally, they are dipped in tin or tin/lead.
Some metals cause more harm than others. Lead is banned in many countries. It may cause cancer and should not be used. Nickel causes allergies for many people and it also may cause cancer. Fumes and mists from metals and acids are always dangerous to breathe. For more information on metals.
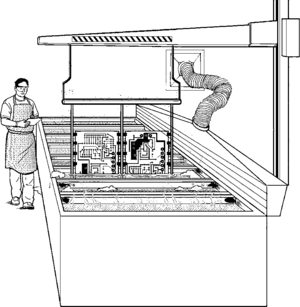
Protect workers in DES and plating areas
- Local ventilation must be both strong and focused enough to pull the fumes from the chemical baths and each machine out of the work area.
- Respirators may be needed to prevent workers from inhaling the fumes that the ventilation does not remove.
- Acid-resistant clothing, boots, gloves that are changed every day, eye protection, and other gear will be needed to protect workers from the dangers of splashes, burns, slips, and other injuries related to working with acids, solvents, and other chemicals.
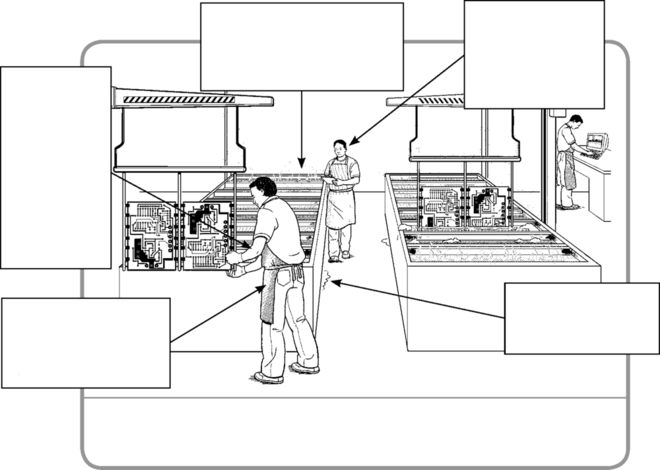
Making a board ready for components
Before going to assembly factories, the boards may go through a number of processes from which employers must protect workers, taking similar precautions as in the DES area. These processes include:
- Solder mask: The boards are coated with a chemical to protect the nonmetal areas from the soldering process.
- Legend: The boards are printed with ink or lasers to show where components will be placed during assembly and to help during repair.
- Removing tin/lead: The tin or tin/lead is stripped with a mixture of nitric acid and ferric ion to expose the copper.
- Final surface finish: Parts are polished so components can be glued on. Boards are dipped in nickel and gold so they better conduct electricity.