Hesperian Health Guides
Assembling the shoes
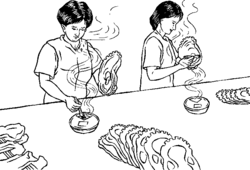
Many chemicals are used to join the sole and the upper together, including primers and glues (see Most glues and primers are harmful to workers). Solvent-based glues and primers contain different kinds of solvents (see Solvents). Water-based glues are made with different chemicals and are considered safer than solvent-based glues. Some of them, especially isocyanates, can still harm workers.
Pay attention to any signs that people are getting sick from primers and glues. Breathing problems, headaches, and fainting are signs that you are breathing in these chemicals.
Contents
To prevent harm while using glues, your factory should:
- replace toxics with less toxic alternatives.
- use closed, mechanical systems to apply glue. If glue must be put on by hand, use containers with smaller openings and smaller tools to apply only as much as is needed.
- store glues and solvents safely, and mix them in a work area with the right tools, work surfaces, and ventilation.
- label all glues in the languages workers speak.
- provide workers with Safety Data Sheets (SDS) including information about the glue, such as ingredients, danger signs for exposures, safety procedures, and so forth, in your language. (See How to get and read an SDS.)
- make sure there is good ventilation (see Chapter 17).
- give gloves, respirators, safety glasses or goggles, and personal protective equipment to workers who need them (see Chapter 18).
- install body and eye wash stations in areas where glues and primers are used, and give first aid trainings on how to handle chemical spills and splashes.
Safer chemicals for the whole factory
The owner of Elegant Top Shoes factory decided to stop using toluenebased glues because toluene is toxic to people and the brand he sold shoes to was pressuring him to change. To replace the glues made with toluene, he found a new glue that was supposed to be safer.
But in one section of the factory, the team leaders still wanted to use the old glue. They said, "The new glue does not work as well," and "The new glue makes the shoe harder to clean."
If the shoes are not clean when they come off the production line, the quality standard of that production line goes down. The line is penalized if it takes too long to clean and finish production of the shoes. Because the pressure to meet production quotas never lets up, the team leaders continued to force the workers on their line to use the toxic toluene glue.
The factory administration knew about this but did nothing to stop it, because the toluene glue was less expensive. Finally, when the problem was pointed out during a factory visit by a representative of the brand that purchased the shoes, they stopped using the harmful glue.
A few months later, workers started to feel sick. They wondered if it was from the new glue. The new glue was water-based and only bonded well when they used a primer that included a chemical called MEK. Although the boss said it was safer than toluene, it made them feel worse more quickly. When the workers asked for and got a safety data sheet (SDS), they found out MEK was dangerous too.
The workers were mad at their supervisors, and the supervisors were mad at the boss. The boss was angry at the chemical salesperson who told him that the glue and primer were safe, and at the brands for demanding he change. He felt he had tried to do the right thing and everyone got mad at him anyway.
The only way to make the situation safer was to install new, more powerful extractors and use better protective equipment. But that cost more money, and most of the workers were hired through a temporary worker agency and would soon be gone anyway.
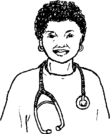
Dangers of finishing
Final finishing of shoes includes shaping and leveling, waxing, coloring, spraying, cleaning, threading, polishing, and packaging.
- Dust from finishing machines must be ventilated away from the workstation. (See Chapter 12: Dust.)
- Polishes, stains, and color dyes may irritate your skin. Solvents used to clean the shoes can quickly harm your health. Work areas must have good ventilation, and workers should have gloves, aprons, safety glasses, masks, and good washing and sanitary facilities.
- Unguarded and unsafe machines that can cut and crush must be repaired. (See Chapter 9: Machine injuries.)
Fire dangers in shoe factories
The solvents and sprays used as glues and finishing materials are usually petroleum-based, causing them to catch fire easily. Being heavier than air, when solvents are not ventilated away they tend to drift toward the floor where they can concentrate. They then create an increasingly dangerous possibility for an explosion, which could be set off by a spark or bad electrical connection. (See Chapter 11: Fire.)
- Use solvents that will not catch fire at low or normal temperatures. Water-based solvents are safer.
- Install good ventilation and local exhaust in spraying booths and drying racks to remove the dangerous fumes from the work area.
- Remove wastes from workstations, as well as other material that can burn, such as rags and cardboard.
- Use fireproof metal containers for solvents and oily wastes.
- Keep aisles and exits open and unblocked.
- Make sure fire extinguishers are full, charged, and of the right type for the materials in your workplace.
- Regularly check electrical equipment to be sure it is in good condition and grounded.