Hesperian Health Guides
Making the soles
Dangers from mixing materials and chemicals to make soles
Most soles are made from ethylene vinyl acetate (EVA), polyurethane, or rubber, both synthetic and natural. These are heated and mixed with many other chemicals while getting rolled into sheets. Putting all the chemicals together creates dust, vapor, and fumes that are all dangerous to breathe.
Workers who measure and mix chemicals may be exposed to chemicals through spills, splashes, dusts, and fumes. One way of reducing the risk of exposure for workers is to use pre-mixed chemicals. Nike, for example, uses a pre-mix process in which the chemicals are measured, mixed, formed into pellets, and packaged, all before they arrive at the shoe factory. The shoe workers then add a packet of pre-mixed pellets into the machine that mixes the rubber or plastic to make the soles. This not only limits exposure for workers but also reduces waste. If the process of manufacturing the pellets at the supplier factory is also safe, it is an improvement for everyone.
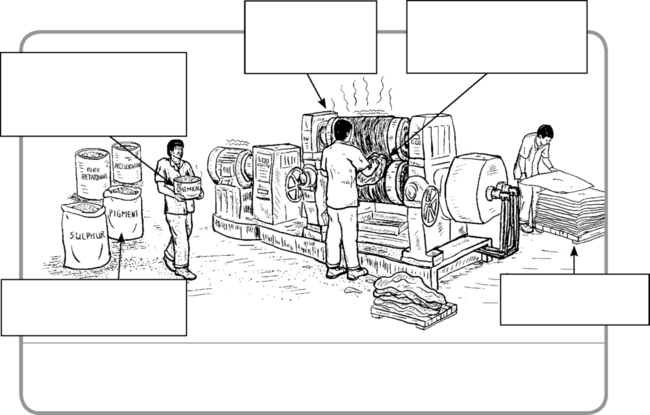
Workers in this area need:
- safe, well-ventilated places to store and mix chemicals.
- good maintenance for both the work area and the machines.
- good ventilation to take heat and fumes out of the work area and factory.
- access to respirators, gloves, and other protective equipment when needed.
Dangers from molding the soles
Soles can be made by putting a sheet of rubber in a mold that is heated and cuts to the right shape. Or the rubber can be injected directly into a mold in an enclosed machine.
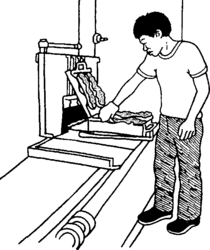
No matter which method is used, when workers remove the soles from the molds, the soles are hot and release fumes from the chemicals used to make them and release them from the molds. The soles continue to release these fumes as they cool in the waiting area.
- Molding machines should have good local ventilation to remove dust and fumes.
- If workers are exposed to fumes, they should tell the boss to repair the ventilation system and demand he provide respirators with the right filters until it is fixed.
- Molding machine temperatures can rise to 150° C or higher. Guards on the machine can protect you from burns.
After the soles have cooled and cured, they are usually not harmful to handle.
Dangers from grinding the soles
Workers grind and clean the soles. Grinding produces a lot of dust that can be harmful to workers. Often, this process takes place inside of semi-enclosed, clear plastic boxes.
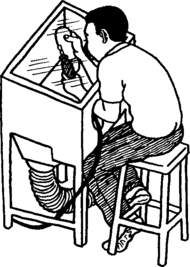
- The box should contain an extractor that removes most of the dust.
- Workers who add and remove soles from the boxes need to have local ventilation. If they do not, they should also wear dust masks.
- Workers should also have gloves and a face shield with goggles, since rubber dust can irritate skin. (See Chapter 18.)
Sometimes grinders are used to rough the surface of soles so glue will hold better. Because this creates harmful dust, newer methods use a water-based detergent to achieve the same thing.