Hesperian Health Guides
Workplace changes to reduce injury
HealthWiki > Workers' Guide to Health and Safety > Chapter 7: Ergonomics > Workplace changes to reduce injury
Contents
Tables that fit you
A table should be the right size and shape for the task you are doing and the right height for you:
- If you are sitting, your arms should rest comfortably on the table with your wrist mostly straight. If the table is too low, you will have to hunch forward straining your neck, back, and shoulders. If it is too high, you will have to raise your arms, straining your shoulders, neck, and upper back.
- A table should be big enough to hold all the materials you need to do your job. It should be high enough to allow your legs to fit underneath.
- A table tilted towards you makes it easier to see your work without bending forward. If you sew heavy fabric, a tilted table might help pull the fabric through the machine.
- Edges should be padded to put less pressure on your arms.
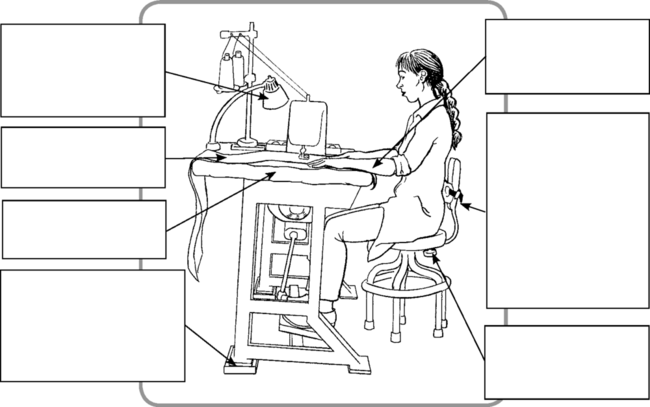
Tables for when you stand
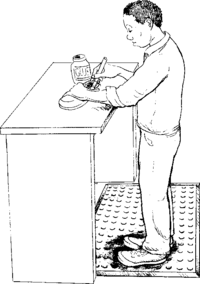
If you work standing, use your elbow to determine the safest height of your table. If you are doing very precise work, your table should be a bit higher so you can rest your elbow on the table. If you are doing assembly work that requires you to use some force, it is better for the table to be a bit lower than your elbow.
The best tables for people who work standing are ones that can be adjusted up or down to fit each person who uses them. Adjustable tables can also make it easier to switch between sitting and standing.
If you can not get an adjustable table, change your table to fit you better. If the table is too short for you, add blocks under it or raise the work closer to you. If the table is too high, you can stand on a platform. Make sure any changes you make to the table are safe, secure, and will not cause new problems.
Soft-soled shoes and padded floor mats can reduce leg pain for workers who have to stand for long periods of time.
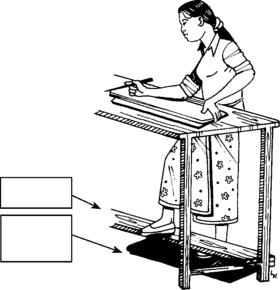
Standing is also easier on your back if you rest one foot on a brick or a block of wood and change positions during the day. You can make a footrest by taping stacked cardboard, paper, or a piece of wood to the floor. Make sure the footrest does not get in the way of a machine pedal and is not too close to electrical connections.
But standing too long is not good for your back either. Use a high stool or a sit-stand chair (see below). Take regular breaks to sit or walk around.
Chairs
A chair should support your legs, hips, back, and body while you work. To be comfortable, a chair needs to fit the size and shape of the worker who sits on it, and have a padded seat and backrest.
![]() |
![]() |
![]() |
Bad: hard chair or stool | Better: chair with cushion and backrest | Best: adjustable, padded chair with backrest |
![]() |
A "sit-stand" chair lets you alternate between sitting and standing with support. |
Adjustable chairs can fit many different people. The chair should be adjustable for height, tilt of the seat and backrest, and height of the backrest. Small changes can make your chair or table fit you better.
Now we have chairs!
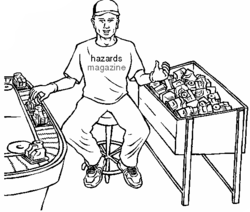
We didn’t have chairs at our factory in the United States. When our backs and knees hurt from standing, we sat on empty buckets. We told our union representatives, and they raised the problem with a joint worker-management committee in charge of preventing injuries. Under our union contract, the committee can demand that the boss make changes to protect workers’ health. Now we have chairs with backrests and foot rails. I change between sitting and standing every hour. And I feel the difference!
If all you have is a stool or a non-adjustable chair, you can still make it fit you better:
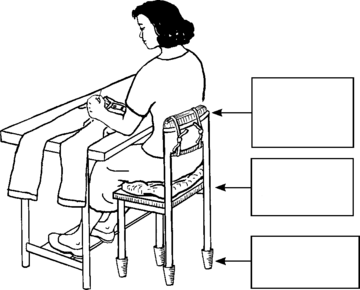
Make the chair taller so your arms can be at a comfortable length from the table: Use items from your workplace to make chairs taller. Garment workers use thread cones and spools. You can use wooden blocks or other materials. Check the cones or other materials for cracks and make sure the chair is stable and does not wobble. You might have to attach them to the legs or make the chair taller by adding a cushion to the seat.
Make the chair more comfortable so it does not hurt your legs and back: Add a cushion to the seat or backrest. To give good support, a backrest should fit against your lower back and help you sit upright, with a slight forward curve in your lower back.
Attaching fabric or other padded material to the hard edges of tables and chairs will also protect you from pressure while sitting or leaning.
If your feet do not touch the floor, add a platform underneath them.
Make a seat cushion
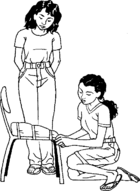
- Use rough material to keep the cushion from slipping. Attach the cushion to the chair with string, tape, or strips of fabric.
- Use a firm cushion. Material that is too soft will quickly lose shape and support.
- Adjust the thickness of the stuffing so you can work at a comfortable height. Too high will make you bend your neck forward. Too low will make you raise your arms or shoulders.
- Make the cushion wedge-shaped to allow your knees to be a little lower than your hips.
Workstations
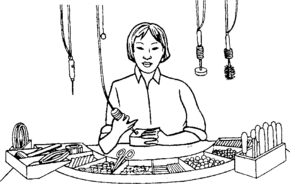
Rearrange your workstation and tools to reduce the amount of reaching and bending you do. Put tools or materials in constant use (such as scissors, drills, and glues) in front or beside each worker in a way that limits reaching to about 40 centimeters (16 inches) or less. That is about the distance between the tip of your middle finger and your elbow.
Workers who sit down can place bins and carts as close as possible to their chairs, or far enough away that they must stand up and move to use the bins. Alternating between sitting and standing reduces body strain during the workday.
![]() |
![]() |
Bending to reach the bin puts strain on the back and shoulders. | Bins are easier to reach if they are beside you at waist height or close to your elbow. |
Add good lighting to your workstation
Workers need proper light to see clearly. Bending, squinting, and straining to see your work can injure your back, shoulders, neck, and eyes. An adjustable task light at each workstation can put more light where it is needed most. For more ideas about improving lighting in the factory, see Chapter 14: Light.
Switches and pedals
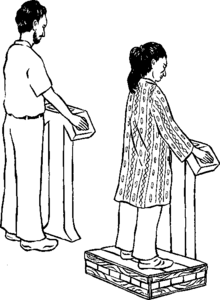
Foot pedals, knee switches, and other controls are safest when you can operate them without using much force.
Machine switches, levers, and handles should be easy to reach without stretching, bending, or raising your arms above the shoulders. You should be able to operate a switch with only a small movement of your arm, leg, or foot.
Foot pedals are best for seated jobs. Raising your foot off the floor every time you press the pedal strains the legs and lower back, especially if you are standing. A pedal wide enough for both feet allows you to use either foot or alternate between feet.
A pedal should be positioned so you can sit or stand at a comfortable distance from the machine. A moveable electronic treadle may be the best choice for machines shared by workers on different shifts.
Pedal-operated machines should have safety systems to protect you from injury if you accidentally hit the pedal.
![]() |
![]() |
The platform helps reduce strain from pressing the pedal, but operating a pedal while standing can hurt your back. | Using a chair or stool can help. |
Tools
Having the right tool that fits you for each task means you can work more accurately, safely, and quickly.
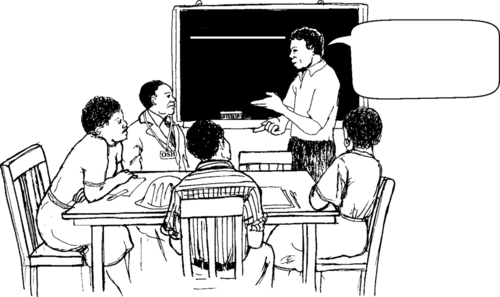
Machine tools
Hand tools
Fit each worker’s unique hands
Most hand tools come in different shapes and sizes, just as workers’ hands also come in different sizes. To help prevent strain to fingers, hands, arms, and shoulders, each worker should use tools that fit the size and shape of her hands.
![]() |
![]() |
![]() |
Tools you hold with your fingers for control and accuracy should be small enough to hold between your fingers and thumb. | Tools you hold with your whole hand for power, such as a hammer, should be large enough so your fingers wrap comfortably around the handle. | Tools with 2 handles should close easily and open on their own. Often they have a spring that pushes the handles back open. |
Designed to make work easier
A tool should be only as large and heavy as needed to do the job. The shape and features of a tool, such as a bent handle or a ratchet, can make repetitive or forceful tasks easier.
Tools with straight handles keep your wrist straight when you point the tool in a direction other than the way your arm points. | ![]() |
![]() |
Tools with bent handles keep your wrist straight when you point the tool in the same direction as your arm. |
Have comfortable handles
A comfortable handle fits in your hand. It is not too large or too small to grip, and does not have sharp edges that press into your fingers or palm. It does not put your hand or fingers in unnatural positions.
With this tool, the thumb has to stretch and work alone to press the trigger. | ![]() |
![]() |
With this tool, the fingers share the work of pressing a wide trigger. The thumb helps grip and guide the tool. |
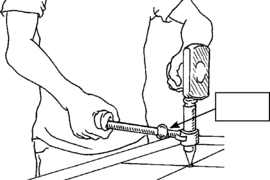
Rubber sleeves over handles can reduce injury from vibration. But they have to fit the tool well. A rubber sleeve can make the tool less stable and increase the danger of injury. A sleeve can make the tool wider. Do not use a rubber sleeve if it makes it harder for you to grip the tool comfortably.
Clamps and handles help you grip tools and parts more securely. Handles also help protect your hands from sharp points and edges.
Balanced weight
A balanced tool is evenly weighted so you do not have to strain to hold the tool in position. Tools should be balanced for the way they are used.
![]() |
![]() |
This drill is unbalanced because the handle is behind the heavy motor. To use the drill you must support the front end with your other hand. | This drill is balanced because the handle is below the heavy motor. This drill can be used easily with one hand. |
Supporting heavier tools with a spring-loaded arm positions them in the right direction for work, so you do not have to pick up, set down, and support the tool each time you use it.
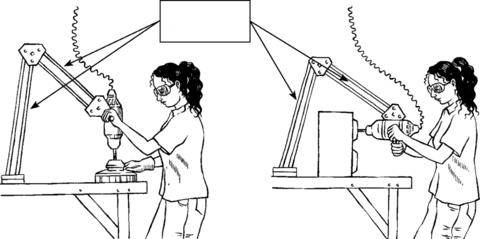
Lifting, carrying, and moving supplies safely
Moving supplies, materials, products, and waste around a factory can be hard work and causes many injuries. Using more machines instead of people to do the work may reduce some kinds of injuries, but may also reduce the number of workers needed to do the job. It is important for workers to discuss how any workplace changes can protect both their health and their jobs.
If you must lift things from the ground, try to lift with the load close to your body, with your back straight and feet stable on the ground. Use your legs to lift your body and the load at the same time.
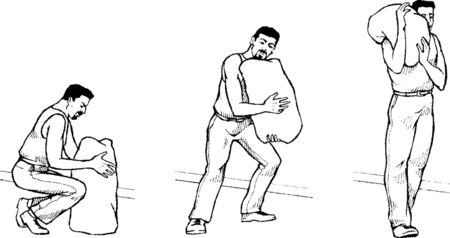
![]() |
![]() |
![]() |
![]() |
![]() |
Divide materials into smaller loads. It might take a bit more time to move them all, but it will be safer and healthier for your body. Employers can tell suppliers they will only buy materials in smaller bags or containers.
Ensure containers have good handles. Also make sure there are no sharp edges on boxes, barrels, bins, and equipment to make them safer to carry without hurting your hands and arms.
Carry balanced loads. They are easier to carry than a load carried on one side. Pack the loads to prevent the contents from shifting.
Make factory surfaces the same height. This reduces lifting from the ground and above the waist. Carts with shelves at the same height as work tables make loading and unloading easier.
Have or make raised, tilted bins and spring-loaded bins. Bin bottoms that rise as the bin empties reduce the need to bend over to reach parts at the bottom of the bin.
Make a spring-loaded cart
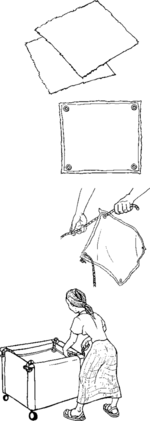
Adding a spring-loaded bottom to a deep cart can make it easier to reach items at the bottom of the cart. The spring-loaded bottom moves up as you unload the contents of the cart.
Materials needed: canvas fabric, grommet-holer or button-holer, 4 strong elastic cords (bungee cords).
- Make a rectangle out of the canvas to be the false bottom for the cart. You may need two or more layers of fabric.
- Make a hole in each corner of the canvas rectangle. A reinforced button hole or metal grommet will last longer than a punched or torn hole.
- Place an elastic cord through each hole in the canvas and secure it. Place the canvas in the cart and secure the other end of the elastic cords to the cart’s top corners.
- Adjust the length of the elastic cords to allow the false bottom to rise to just below the top of the cart when it is empty. The cords should stretch to the bottom when full. If your cords don’t do this, use a different kind or different length cord.
Use mechanical or power tools
![]() |
A hand truck can help you move heavy materials, but do not overload it.
| |
A passive conveyor allows you to push parts and boxes over rollers between workstations instead of carrying them by hand or cart. | ![]() | |
![]() |
A rail system allows you to push or pull parts or tools around the work area from a rolling holder. This is especially useful when things need to hang, such as finished clothing or material ready for dipping or spray coating. |
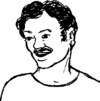
Make sure moving equipment has good wheels
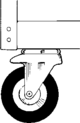
Wheels make moving easier. Wheels that are kept in good repair and changed when they are broken will make hand trucks, trolleys, carts, and bins more useful.
Wheels covered with rubber or a similar plastic last longer and are easier to move than uncovered metal wheels.
Carts are easier to move when the back wheels swivel.
![]() |
Larger wheels are easier to push and maneuver, especially on rough floors and over gaps in the floor. |
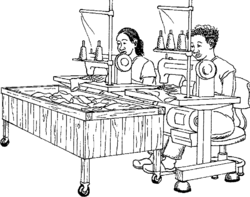
A workstation bin on wheels can be used to bring supplies and remove waste in the same container, reducing the need to move things from one bin to another.
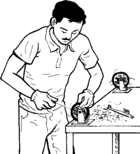
Wheel brakes help workers control movable equipment and keep it from moving unexpectedly. Moveable bins, carts, and tables should have brakes on the wheels. You should be able to easily lock or unlock wheel brakes with your foot. You should not have to use much pressure or bend over to do this.
Wheels need to be cleaned often to keep turning smoothly. You can remove dirt and debris from a wheel with a stiff brush, but replacement wheels are needed when a wheel can no longer be cleaned or repaired.
A parade of broken, squeaky carts
Our factory creates a lot of waste that makes the factory floor wet and sticky. When workers move products around the plant, the waste on the floor gums up the wheels so the carts do not roll smoothly and get banged up. The wheels also rust because they are rarely cleaned or repaired.
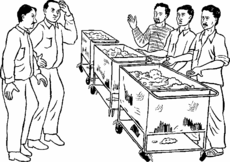
The union had asked for new carts several times, but the boss didn’t respond. One morning, we lined up all the carts in front of the door to the office. Everyone who passed through that door had to look at the broken carts. When the managers arrived, they didn’t understand why the carts were in front of the door. The director came and asked what was going on. He ordered us to remove the carts, so we did.
The carts made a terrible noise as they lurched forward, bumping into each other because the wheels would not turn smoothly or straight. The director glared at the managers and slammed the door as he returned to his office. New carts arrived 3 weeks later!
Maintenance and repair
Workers do their jobs best when their workstations, tools, and equipment are clean and in good repair. Dull cutting tools, machines clogged with dust, and unstable furniture can cause strain and other injuries. Poorly maintained machines are noisier, less efficient, and break down more often. Good maintenance is good for safety and good for business.
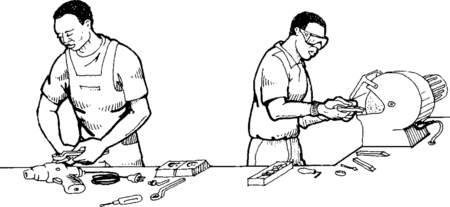