Hesperian Health Guides
Working safely with machines
HealthWiki > Workers' Guide to Health and Safety > Chapter 9: Machine injuries > Working safely with machines
![]() |
An experienced worker can train new workers to use machines safely. |
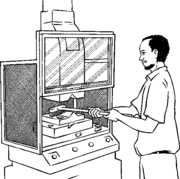
Each worker should be trained to safely use every machine she operates. Because operating a machine often includes tasks such as maintenance, cleaning, and making adjustments to the machine, be sure you are trained to do this safely as well.
Contents
Clearing jams and debris
If you must clear a jam or remove debris from inside a machine, be very careful. Use methods that prevent injuries. For example, use tools and avoid putting your hands or body in a dangerous area. If you do not have the right tool, or if you cannot clear the machine with the tool you have, be sure to disconnect and lock out the machine before you get near a dangerous area. If you are not trained to lock out and tag out the machine, do not try to clear the jam or debris yourself. Get help from a worker who is trained to safely repair the machine.
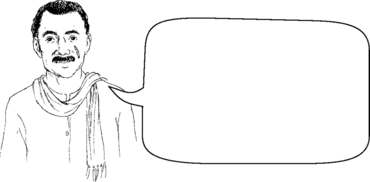
Protect workers from machine injuries
Machine guards prevent a worker’s body or clothing from getting caught or cut by moving parts, from getting burned by hot surfaces or materials, and from being injured by materials or parts that can break off or fly out of a machine.
Guard the dangerous areas of a machine:
|
![]() sharp cutting edge needs a guard |
|
![]() nip points that can catch clothes or body need a guard |
![]() grinding wheel needs a guard |
|
|
![]() How would you change this workstation to protect the worker from injury?
frayed wires
steam
hot iron |
There are many different kinds of guards and no one kind of guard is best for all machines and all tasks. Workers must be protected during regular production, during setup for a new product run, when re-tooling or making adjustments to machines during use, and when clearing parts that get jammed.
All machine guards should be inspected and tested regularly to be sure they are in place and working.
Fixed guards
A fixed guard prevents a worker’s body from getting near dangerous areas of a machine, or from being hit by broken parts flying out of a machine
![]() guards for cutting blade
metal mesh glove
|
![]() eye shield
needle guard
guard for drive belt |
Guards on a fabric cutting saw and protective glove | Guards on a sewing machine |
![]() press guard
guard over moving parts
heat guard on steam pipe | |
Guards on a garment press |
Getting the boss to replace needle guards
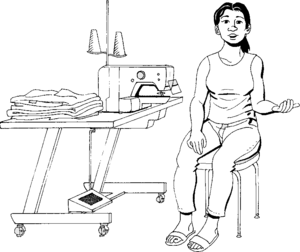
My name is Cecilia. I work in a large garment factory in Mexico. Workers in my factory have organized for many years, and we have won changes that make our work safer and the workplace better for everybody. We have a good relationship with our boss. He understands that many of the things we have requested to make our work safer benefit him too. But he also sees that we are united and strong and that we are going to fight for better conditions even if they are not "convenient" for him. Sometimes he agrees to some of our demands right away instead of resisting. That is how we got new needle guards on our machines.
Our machines had guards to keep our fingers from getting caught under the needle. But the guards often broke. At first, when a needle guard broke, we just kept sewing. We have to meet a production quota and stopping can make us miss it and lose our bonus for that day. The boss would see us working without the guards and think, "they can work without them, they don’t need them," and then he would not replace them. But without the needle guards, several workers injured their fingers badly.
We needed to act! We work very fast with powerful sewing machines and they need to have guards. The injured workers led the campaign. We told the boss that we would stage a sit-in if he did not replace all the broken guards and make a plan to ensure that guards are replaced promptly when they break. The boss knew a sit-in would cost him a lot of money and he did not want to pay the health costs for injured workers. Besides, needle guards are cheap and easy to replace. So he agreed to keep guards on all the machines and extras in stock. Now when a needle guard breaks, we can have it fixed the same day. Since we made this change, no workers’ fingers have been seriously injured by a needle.
Adjustable guardsSome guards can be adjusted for different uses and materials. They protect workers only if they are adjusted properly and used. But because they can be adjusted, they are easy to remove. Do not let your boss remove or disable these guards to speed up the work and meet unsafe production goals. Take the time to make the adjustments and save your fingers — and your life! |
![]() clear guard over blade
saw blade
Saw for cutting wood with adjustable guard
|
Interlocking guards
An interlocking guard turns off power to the machine when it is not in place. A worker can remove the guard to safely adjust or clear a machine, and then replace the guard to safely restart it. Removing an interlocking guard does not make the machine safe to repair — you still need to lock out and tag out machines for safe repair|lock it out and tag it out first.
Movable barriersSome machines have a gate that opens to feed new material into the machine only when the machine is turned off. That way, the gate will not close, and the machine will not turn on, if a worker’s hand or arm is in the way. Automatic shutoff devicesMachines with doors or gates that open and close often have safety controls that cut off power to the machine when the door is open. Automatic shutoff devices must be regularly maintained and tested to be sure they always work. |
![]() gate will not open if machine is on Metal press with movable gate |
Two-hand controlsMachines with 2-hand controls will start only when you push 2 buttons at the same time. These controls are separated so you must use both hands to push them. While excellent for the worker who uses the controls, this does not prevent other workers near the machine from getting caught by moving parts. |
![]() |
The worker must use both hands to close the press. |
Light curtains and presence-sensing matsA light curtain is made of many rows of light that sense when a worker gets too close to a machine. When you cross the light curtain, the machine automatically shuts off. A presence-sensing mat shuts off a machine as soon as someone steps on the mat. Light curtains and presence-sensing mats must be far enough from the machine so you cannot reach the danger zone before the machine stops moving. |
![]() edges of light curtain
edges of light curtain
beams of light
Machine with light curtains |
Covered foot pedalsMany machines start when someone presses a foot pedal. If a person presses the pedal by mistake or if something falls on the pedal, the machine can start while a worker’s hands are inside. A protective cover over a foot pedal can help stop this from happening. |
![]() foot pedal cover |
Restraints and pullbacks
A restraint is a strap tied to a worker’s wrist or arm that keeps her hands away from the dangerous areas of a machine all the time. A pullback allows a worker’s hands to enter a dangerous area to feed and remove material while the machine is stopped. When the machine starts, the straps pull her hands away from the dangerous area.
Restraints and pullbacks must be adjusted each time a different worker operates the machine. Some countries ban restraints and pullbacks because they are unsafe in emergencies, making it difficult for the worker to leave her machine quickly. They are also humiliating. |
![]() metal plate
tool feeds metal plate into the press
danger area
pullback |
Protect workers with personal protective equipment
The boss must provide workers with equipment and clothing that can help protect them from machine injuries. These are not a replacement for having good guards on the machines.
Protect your face and eyes. Safety glasses and face shields protect you from flying debris, broken parts, and splashes of chemicals or hot materials. If you are working with hot materials, wear face shields made from material that will not melt, burn, or shatter from heat. When you remove the face shield or goggles, tip your head forward and close your eyes to prevent hot particles or debris from falling into your eyes. Hats, hair ties, and hair nets keep your hair from getting caught in moving machine parts.
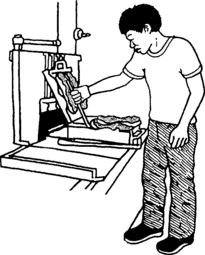
Protect your hands. Use gloves. Wire mesh gloves are used to protect workers from being cut by blades. Leather or fabric gloves and sleeves protect your skin from sharp edges. If you are working with a hot machine or material, use gloves made of leather or other material that will not pass heat to the skin, will not melt, and will not catch fire. If you are working on a machine with moving parts, wear tight gloves that will not get caught in the machinery. Always change gloves right away if they get wet or covered with chemicals.
Protect your body and feet. Coveralls and aprons protect your clothes and skin from dust and chemicals, and help prevent clothes from getting caught in moving machine parts. Wear long clothing and closed shoes made of leather, wool, or canvas that does not burn easily or melt. If you work with hot liquids, such as chemical or electroplating baths, a heavy rubber apron and rubber boots will keep splashes from burning through your clothes.
For more information on the different kinds of personal protective equipment (PPE), see Chapter 18.
Lock out and tag out machines for safe repair
Workers who clear jams or repair machines need additional protection, because they must work inside the dangerous areas of a machine. To prevent a machine from starting or moving during repairs, workers need the time, training, and tools to:
- Lock out the machine so it cannot start or move. This means not only disconnecting the electricity from a machine but also disconnecting any belt or drive shaft from another machine that might drive the machine being repaired.
- Block out the machine so water, chemicals, or other materials that flow into it are completely blocked or shut off during maintenance and repair. Also, energy stored in springs, in electronic parts such as capacitors, and as water or air pressure in pistons, hoses, and pipes must all be released or blocked.
- Tag out the machine so other workers know the machine, power cord, and belts were disconnected on purpose and they should leave them alone.
Employers are responsible for making lock out and tag out required, easy, and routine.
Guidelines for lock out
Every factory should have a lock out program to prevent repair and maintenance workers from being killed or injured by a machine. A good lock out program will follow these guidelines:
- A worker never repairs or maintains a machine until all the energy sources to the machine are disconnected, blocked, and locked. This will prevent the machine from starting up unexpectedly.
- A repair worker attaches a tag to his locks that says why the machine is locked out, says who is responsible for the lock out, and shows other workers and supervisors not to reconnect and start the machine.
- The repair worker has the only key to his locks and is the only one who can unlock the machine, remove the blocks and tags, and reconnect the power.
- If more than one worker is repairing the machine, each must attach his or her own lock and tag and remove them when done.
- All workers are trained on why lock out procedures are used and why respecting these rules is important.
Lock out instructions for each machine
Some factories have many kinds of machines and several types of the same machine. To make each machine safe for repair, you need to know exactly how to disconnect it and block it. Putting individual lock out and block out instructions with pictures on each machine helps workers be sure they are doing it the right way for each machine.
Reinstall guards and other safety devices
Machine technicians and maintenance workers sometimes remove guards and disconnect safety devices while they work on a machine. Always reinstall the guards and reconnect safety devices before unblocking a machine and reconnecting the power.
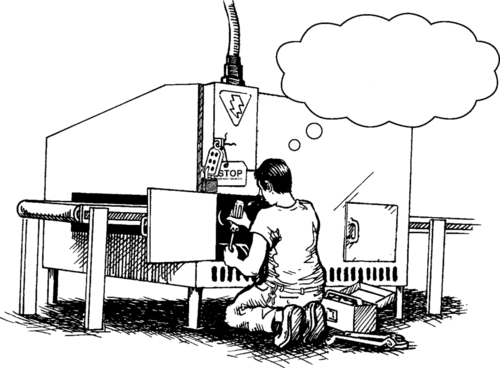